На одном из предприятий Подмосковья по производству буровой техники в октябре 2013года запущен в эксплуатацию комплекс автоматизированного оборудования для изготовления буровых штанг диаметром от 89 до 273 мм с толщиной стенки от 18 до 32 мм, длиной до 12000 мм и массой до 2500 кг. Трубы и наконечники к ним выполнены из среднеуглеродистой легированной стали ст. 30-35ХГСА или сталей 40Х, 38ХМ, 40ХН. На автоматизированном комплексе за одну установку выполняют следующие технологические операции: предварительную мехобработку трубы под запрессовку наконечника, индукционный подогрев трубы до температуры 300° С, горячее прессование наконечника, сварку стыкового шва по разделке С20 наконечника с трубой, последующую мехобработку сварного соединения, замедленное охлаждение.
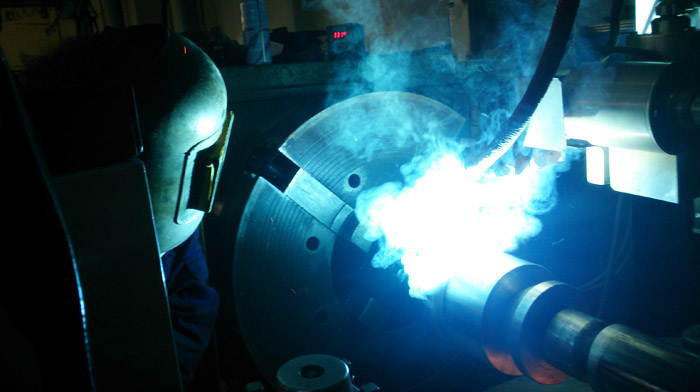
Все технологические операции выполняются одним оператором , который прошел обучение в процессе монтажа и наладки комплекса.
Комплекс смонтирован на базе трубонарезного станка марки 1А983 с модернизированным электроприводом и портальной сварочной установки с подвесным автоматом марки «ВОСХОД» для электродуговой сварки проволокой диаметром 1,2-1,6 мм в смеси газов. Система управления комплексом объединяет работу всех функциональных узлов: продольного, поперечного и вертикального перемещений автомата с ходами 2500 мм, 2х540 мм, вращение изделия с плавно-регулируемой сварочной скоростью, тонкую регулировку положения водоохлаждаемой сварочной горелки в двух плоскостях в пределах +- 25 мм, поперечные колебания горелки с регулируемой частотой и амплитудой и с регулировкой задержек по краям. Источник сварочного тока - ВДУ-506ДК, блок замкнутого водяного охлаждения, работающие на номинальных режимах с ПВ 100% при сварке труб диаметром 273 мм и термозащитные пояса, обеспечивают силовую часть комплекса. Перепрограммируемый контроллер сварочного автомата содержит в памяти 10 технологических программ, что является достаточным для обеспечения программно-управляемых процессов сварки всех типоразмеров штанг. Смена программ оператором выполняется путем назначения на пульте управления комплексом диаметра трубы и включением соответствующей программы на пульте сварочного автомата.
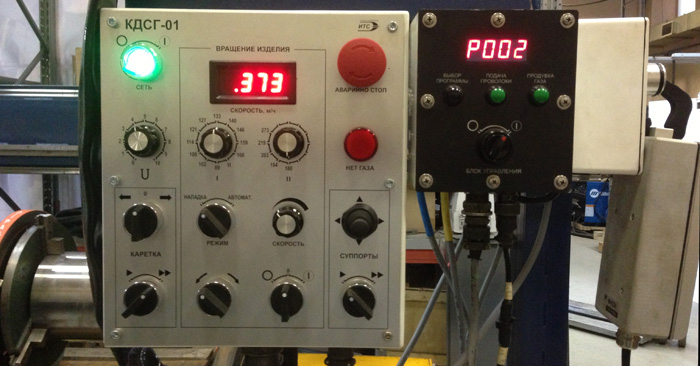
Технологическая часть работы содержит операционные технологические процессы для сварки 6-ти групп штанг, объединенных по геометрическому принципу – поперечные сечения разделок находятся в диапазоне 25-30%, что позволяет выполнять сварку на одних и тех же запрограммированных режимах, отличающихся количеством проходов – от 2 до 9. Время сварки каждого прохода зависит от диаметра трубы и колеблется в пределах от 90 до 270 секунд.
При сварке бесконтактным оптическим пирометром осуществляется непрерывный контроль температуры в зоне 40-50 мм от сварного шва. При повышении температуры свыше 350-370 °С сварку очередного прохода прекращают для охлаждения до температуры 240-250 °С. После выполнения последнего облицовочного прохода по горячему шву выполняют снятие заподлицо усиления, выполняют нагрев стыка для высокого отпуска после чего сварной стык укрывают термозащитным поясом. Для обеспечения равнопрочности сварного шва с основным металлом принята электродная проволока марки НМТ 1000 S-G диаметрами 1,2мм для труб 1 и 2 групп и 1,6 мм для остальных типоразмеров.
Хим. состав металла проволоки: С-0,1%; Mn-1,6%; Si – 0,7; Cr-0,6%; Ni-0,6%. Предел прочности, предел текучести и пластичность сварного шва соответственно составляют 770,690 кг/мм2 и 20%, что соответствует механическим характеристикам основного и электродного металла. Разрушение соединений при испытаниях на растяжение на всех образцах происходит по основному материалу на значительном удалении от зоны термического влияния.
При приемо-сдаточных испытаниях сварены и проверены ультразвуковым контролем сварные швы на трубах 89,0; 180,0; 273,0 мм. Дефектов в сварных швах не обнаружено. Комплекс принят в эксплуатацию.
Разработанная технология многопроходной сварки тел вращения диаметром от 80 мм и выше, изготавливаемых из среднеуглеродистых низколегированных сталей, может быть рекомендована для других производств. Комплекс автоматизированного оборудования в т.ч. с применением имеющегося на предприятии заказчика механического оборудования, рекомендован для тиражирования.